Roofing Applications
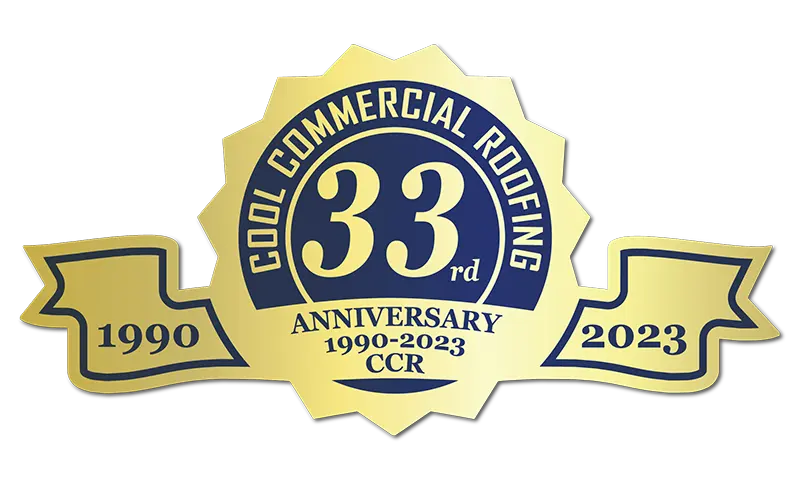
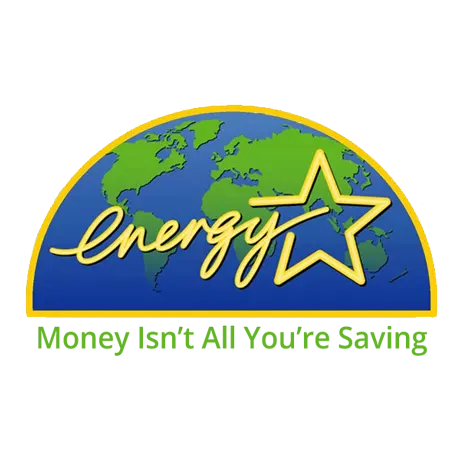
Energy Efficient Commercial Roofing With 35+ Years Of Experience
SINGLE-PLY ROOFING SYSTEMS
Single Ply Roofing Membranes have grown in popularity over the past 60 years for use on commercial buildings. Single-ply roof membranes are lightweight, cost-effective, easy to install and durable. They work well for a variety of projects on roofs of all shapes and sizes, including exposed roofs, green roofs, cool roofs, ballasted roofs and more. They are used in a wide range of applications from large scale commercial projects such as airports and factories to a private house rooftop.
Single Ply Roofing Membranes Are a Popular Choice Because They Are…
- Durable
- Fire resistant and fire retardant
- Chemical resistant
- Resistant to UV and natural elements such as harmful micro-organisms
- Eco-friendly
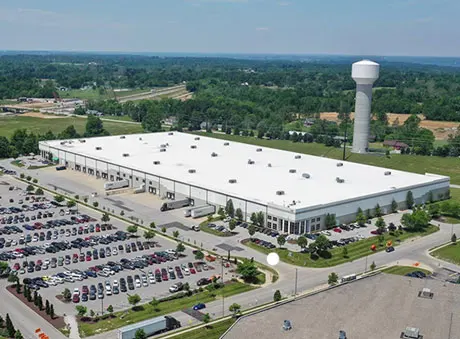
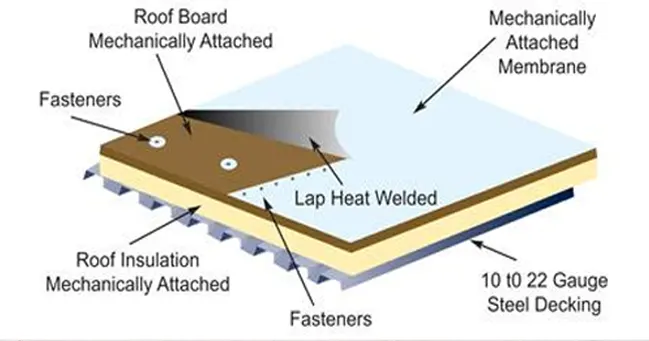
Single Ply Roofing Membranes are composed of four basic elements:
- An insulation layer
- A single-ply membrane
- Mechanical Fasteners
- Flashings
TYPES OF SINGLE-PLY ROOF SYSTEMS
Single-ply roofing systems utilize flexible sheets of thermoset or thermoplastic membranes. Both membranes offer unique advantages and disadvantages. For example, thermoplastics are highly reusable as they can undergo melting numerous times, while thermosets remain in a solid state after curing. The three main types of compounds used in single-ply membrane systems are:
- Thermoplastic polyolefin (TPO): a thermoplastic
- Polyvinyl chloride or polymerized vinyl chloride (PVC): a thermoplastic
- Ethylene propylene diene terpolymer (EPDM): a thermoset
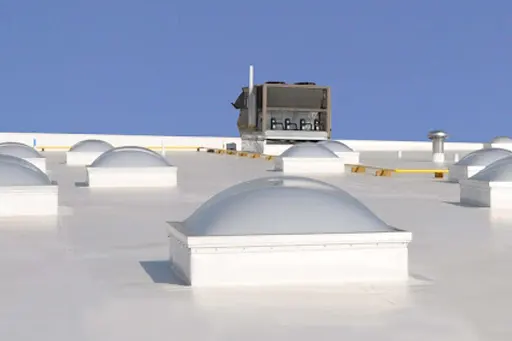
TPO Membrane Roofing Thermoplastic or Flexible Polyolefin (TPO) Membranes
TPO membrane roofing systems have rapidly grown in popularity in the commercial roofing market. These systems feature a single layer of synthetic thermoplastic combined with reinforcing scrim that provides a naturally reflective surface that resists UV radiation penetration and wear. The roofing material is available in rolls with widths of 10, 12, or 20 feet and can be installed using mechanical or adhesive attachment with heat-welded seams. A TPO membrane roofing system’s life span ranges from between 15–30 years.
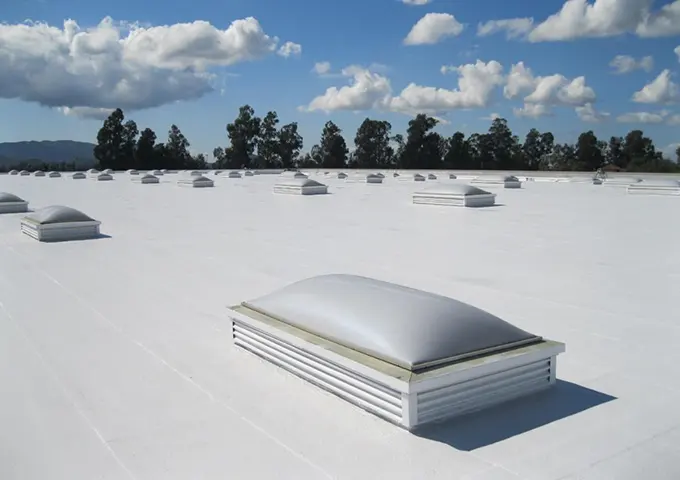
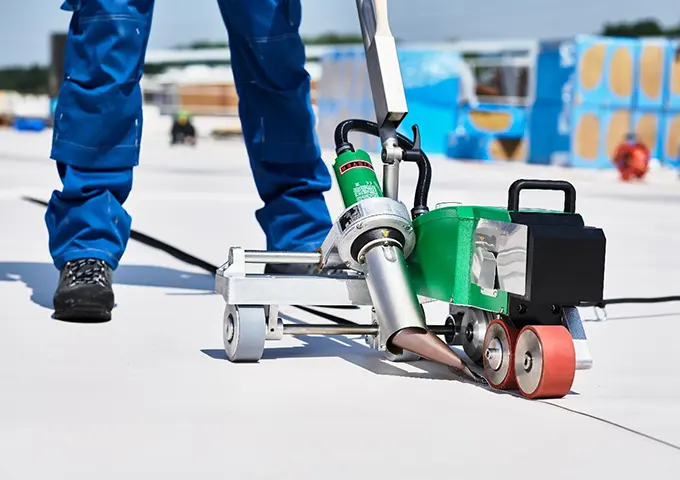
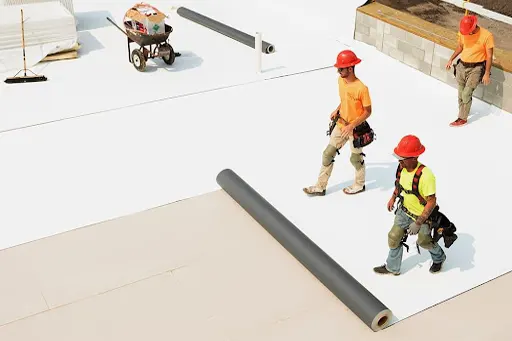
ADVANTAGES OF TPO SYSTEMS
- High chemical resistance
- Suitability for direct application on such substrates, as old bitumen, EPS and XPS insulation (polystyrenes)
- Availability of products for exposed roofing applications with high fire ratings / extended fire resistance
- Plasticizer free (no migration / contamination or leaching)
- Long life expectancy
- Easy to repair
- Homogeneous hot air welded joints
- Easy to handle on site
- Suitable for use and exposure in different climatic conditions
- Fast installation independent of the weather
- Outstanding ecological profile
- Flame-free installation
- Recyclable
- Proven track record since 1989
PVC Membrane Roofing Polyvinyl Chloride (PVC) Membranes
PVC is a synthetic, thermoplastic polymer composed of polyvinyl chloride. It exhibits several advantageous material properties, including resistance to wind, moisture, fire, and chemicals. PVC roofing material usually comes in rolls of 50–100 feet long and 5–12 feet wide. It can be installed using full adhesion, mechanical fastening, or ballasting and seam welding methods. The lifespan of a PVC roof system installation ranges between 15 and 30 years.
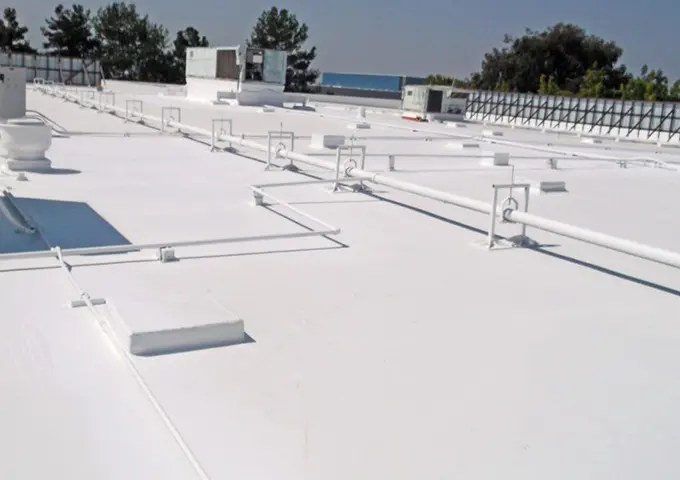
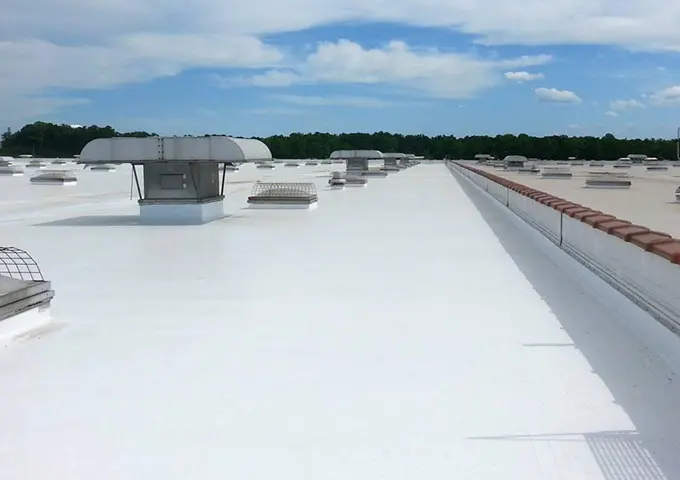
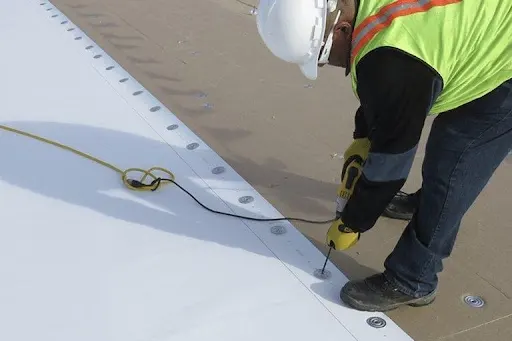
ADVANTAGES OF PVC SYSTEMS
- Established technology with the longest track record
- Availability of products for exposed roofing applications with high fire ratings / extended fire resistance
- Easy to repair
- Possibility of customized design solutions (colors, profiles, and roof graphics)
- Homogeneous hot air-welded joints
- Easy to handle on site
- Suitable for use and exposure in different climatic conditions
- Fast installation independent of the weather
- Good vapor permeability
- Highly flexible
- Flame-free installation
- Recyclable
- Proven technology for over 50 years
EPDM Membrane Roofing
EPDM Membrane Roofing
Composed of two main ingredients—i.e., ethylene and propylene (derived from oil and natural gas)—EPDM is a synthetic rubber. EPDM membranes come as large, black or white rolls with widths ranging between 7.5–50 feet (10 feet being the most common) and thicknesses of 45, 60, or 90 mils. Roof systems which use this material typically have life spans ranging between 10 and 25 years. Common installation methods include full adhesion, mechanical attachment, or ballasting followed by gluing or taping of the seams.
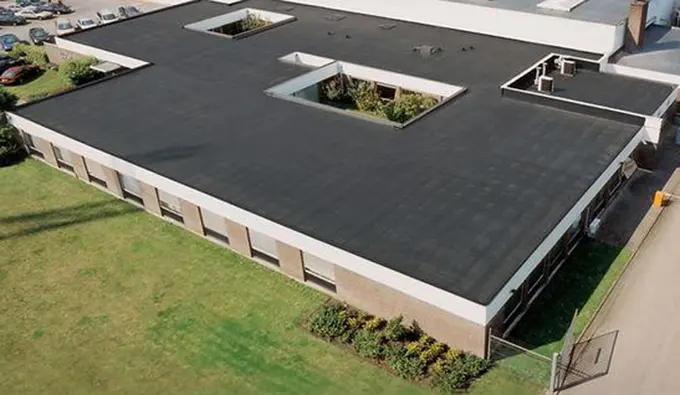
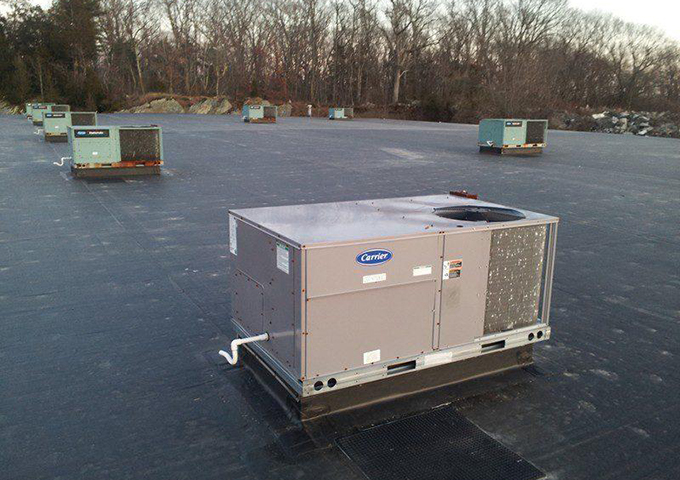
ADVANTAGES OF EPDM SYSTEMS
- Resistance to hail and abrasion
- Durability under extreme weather conditions
- Flexibility in cold weather climates
- UV radiation resistance
- Flexible membrane allows for easier installation, especially at flashings and penetrations
- Cost-effectiveness
ROOF COATINGS
Coatings, when properly applied, are very effective at eliminating leaks in existing roof systems as well as prolonging the useful life span of the roof. There are generally three types of roof coatings you can choose from when restoring your roofing system. These include silicone, elastomeric, and acrylic.
A roof coating is a cost-effective option that eliminates full roof replacement. Like Single-Ply roof membranes, coatings are highly reflective of the sun’s UV rays and as a result are very energy efficient.
Perhaps the greatest benefit of commercial roof coatings is the fact that they can be recoated at the end of their useful service, and thereby extending their service life by 10, 15, even 20 years longer. When a coating reaches the end of its initial life, simply power wash the roof and install a new layer of coating over top of it. You can get a new roof coating, a new warranty, and up to 20 more years of protection for a fraction of the cost of replacing the roof.
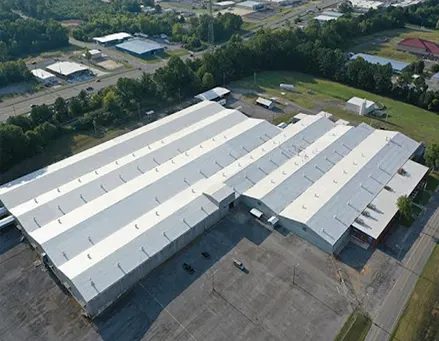
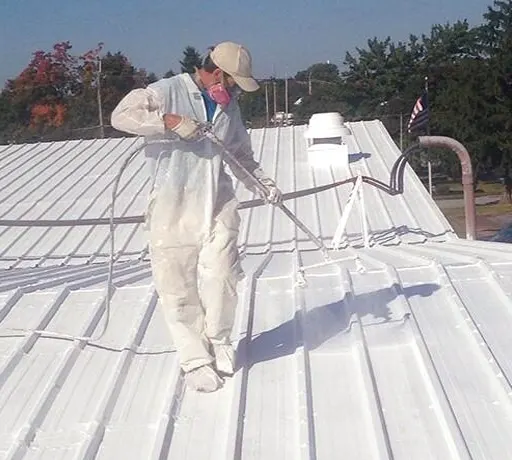
WHAT ARE THE ADVANTAGES OF ROOF RESTORATION VS ROOF REPALCEMENT?
Commercial roof restoration is a cost-effective alternative to complete roof replacement. Roof restoration returns the original roof to a serviceable condition and extends Warranty up to 10-20 Years.
Roof restoration eliminates the need for a costly tear-off of the existing roof system. Building codes in most jurisdictions prohibit more than two roof systems being installed on an existing structure. Restorative coatings are considered a maintenance procedure and therefore can be applied directly on the existing roof system. Because coatings are considered a maintenance procedure the entire installation cost can be expensed within the taxable year that it occurs.
Once the proper cleaning and preparation protocols have been completed the restorative coating is installed on the existing roof structure. Based on existing job conditions and roof design the restorative coatings can be applied by brushing, rolling, or spraying.
WHAT IS AN ELASTOMERIC ROOF COATING?
Elastomeric coatings are fluid-applied roofing membranes that are similar in appearance to paint, but unlike paint they are capable of expanding to twice their original length (100% elongation) and then recovering back to its original dimension. These thermal characteristics and chemical properties make restorative coatings an ideal protective covering for most roof surfaces.
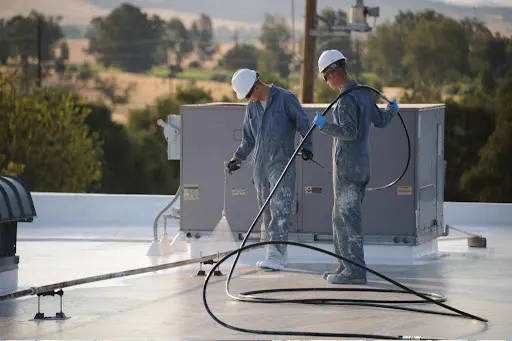
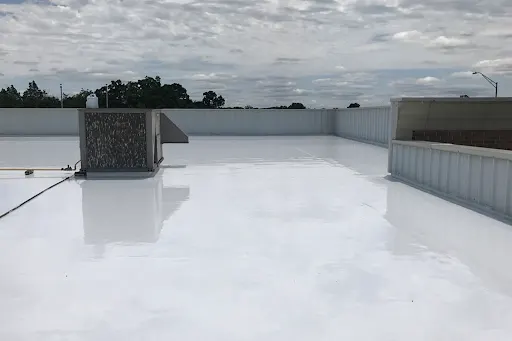
Elastomeric roof coatings are an attractive roofing option for many reasons, such as:
- It’s more cost-effective than completely removing your existing roof.
- The installation process is relatively fast and non-disruptive to building operations.
- They eliminate roof leaks.
- They create a monolithic, seamless, edge to edge, roof system.
- They extend the useful service life of the existing roof.
- The white reflective color cools the building and reduces HVAC energy costs.
- They come with a new 10-20-year warranty.
- They can be reapplied at the end of the warranty period.
- They 100% Tax Deductible In Year 1 under IRS Section 179.
Life-Cycle-Cost Savings: At the end of the warranty period the coating can be reapplied, and the warranty extended for another 10-20-Years.
WHAT ARE THE THREE TYPES OF ELASTOMERIC COATINGS?
Acrylic – is a water-based elastomeric coating that is formulated to be applied to roofs with a slope. Acrylic coatings are formulated with a high a solids content. They are more reflective than their counterparts, making them a better choice for extreme UV climates. Many acrylic coatings also include potent biocides that deter mildew and mold growth.
Silicone – is a silicone resin-based elastomeric coating that’s 96% solids. This means 96% of what goes down on your roof will stay on your roof. Silicones perform great on flat roofs because they can withstand ponding water. Silicones are a middle-of-the-road coating in terms of performance and price. The high solids content also allows silicone elastomeric coatings to be highly UV resistant. Silicone coatings are twice as resistant to weathering as acrylics, resulting in a longer lasting solution.
Polyurethane, or urethane, coatings are the most impact resistant compared to the other elastomeric coatings. This durability lends itself well to roofs with higher-than-average foot traffic. They are also well suited to withstand the expansion and contraction of roofs during thermal changes. Urethane coatings are not recommended on roofs with standing or ponding water. Urethane coatings are expensive when compared to the other two coatings.
METAL ROOF SYSTEMS
Popular Types Of Metal Roofing Sytems:
- R-PANEL
- BUTLER MR-24 STANDING SEAM.
Metal roofing has the reputation of only being used on large industrial or commercial structures. While it’s true that metal is a good option for these applications, metal roofing goes far beyond this with use on homes, architectural buildings, and agricultural structures.
The level of upkeep needed to maintain a metal roof is generally minimal, especially if the roof was correctly installed.
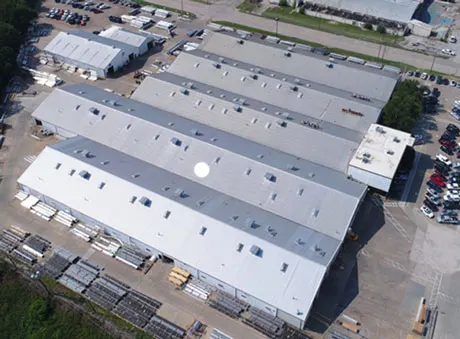
R-PANEL
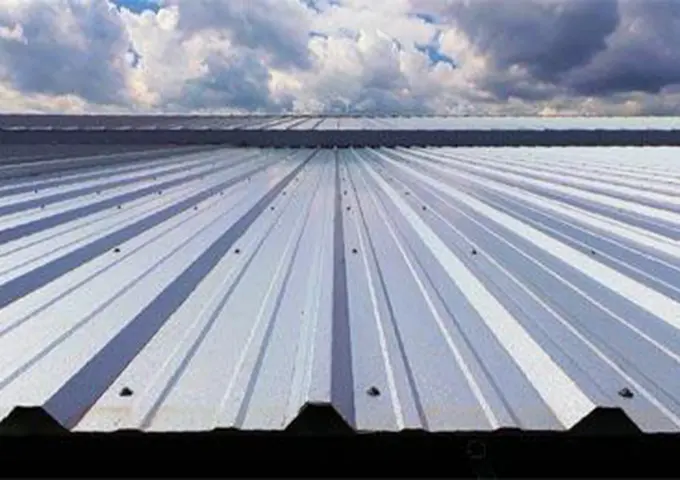
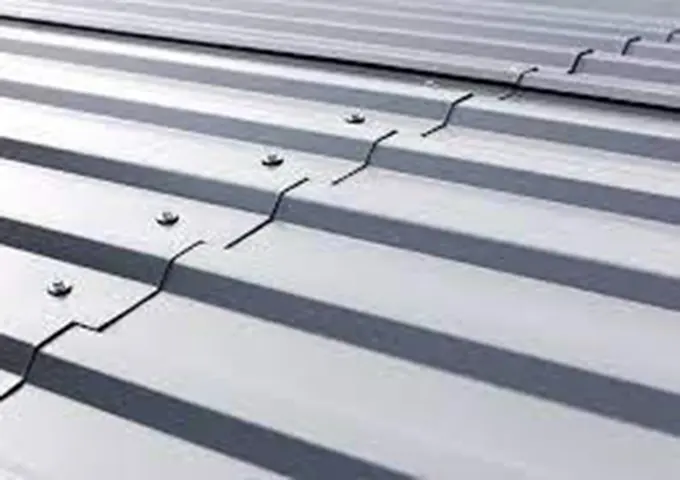
BUTLER MR-24 STANDING SEAM
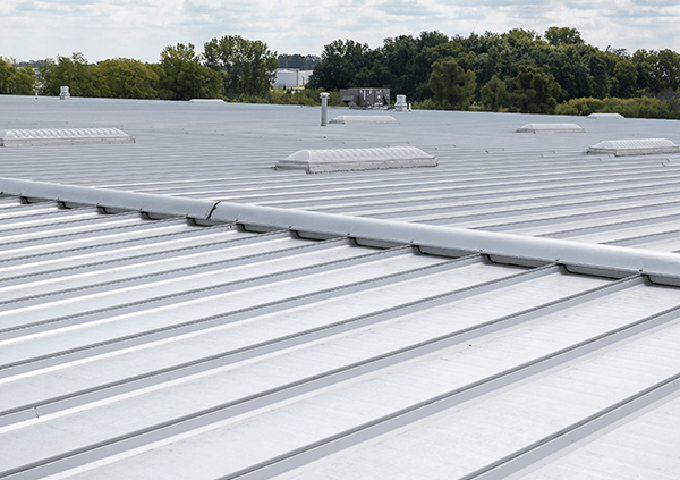
STANDING SEAM
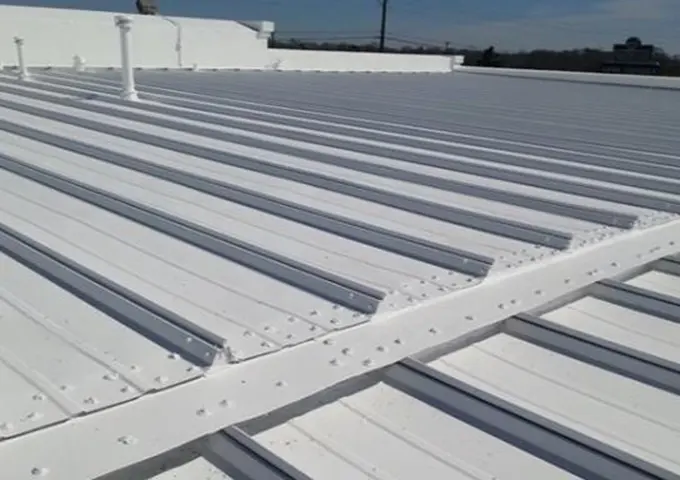
STANDING SEAM
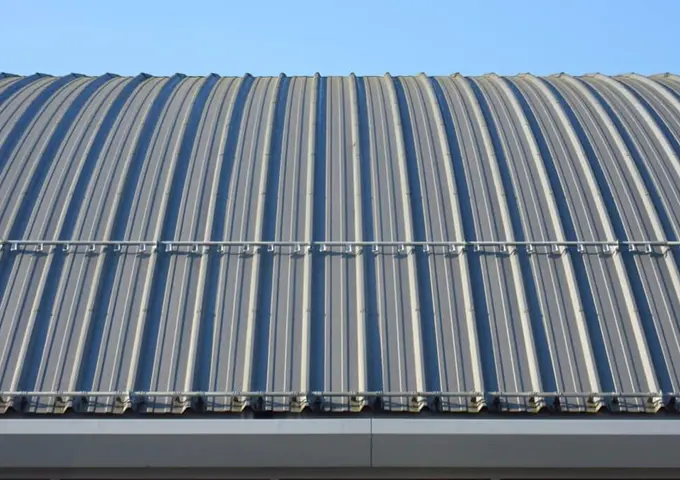
Asphalt Based Roof Systems
BUILT-UP ROOF SYSTEMS (BUR)
Built-up roofing, also called BUR, is the most common roofing material used on low-slope roofs. Built-up roofing is nothing new. The concept been around for over 100 years, although the materials and its installation techniques certainly have evolved during that time. Modern built-up roof systems incorporate a rigid board insulation layer for improved energy efficiency.
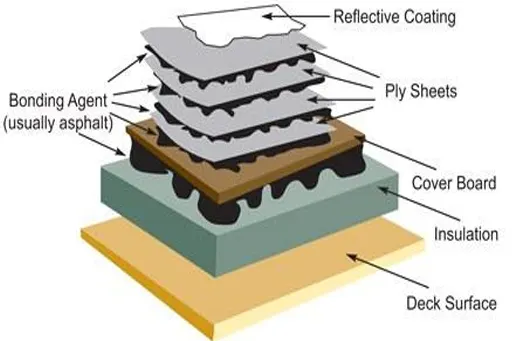
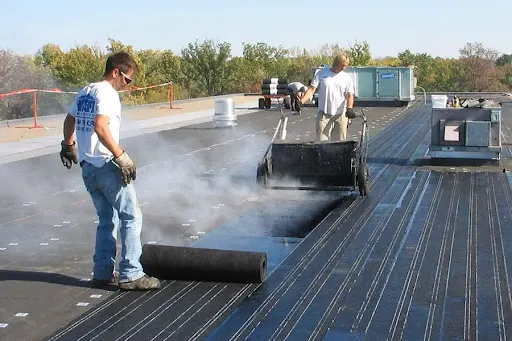
Built-Up roofing consists of multiple layers of material that are laminated together with hot liquid asphalt. BURs are generally created with four basic components in many layers and combinations:
- Base sheet – fiberglass, asphalt coated organic sheet, or asphalt coated venting sheet, etc.
- Felts or fabrics – coal or tar saturated organic felt, cotton fabric or burlap (three or four layers may be used)
- Bitumen – Hot liquid asphalt
- Surfacing component – gravel, asphalt, granualized minerals, or fiberated coatings
A layer of gravel, or small stones, is applied on top of the final coating of asphalt to protect the roof from the elements, including ultraviolet (UV) rays and hail. The gravel is embedded into the top coat of asphalt (known as a flood coat), which helps the gravel stay in place.
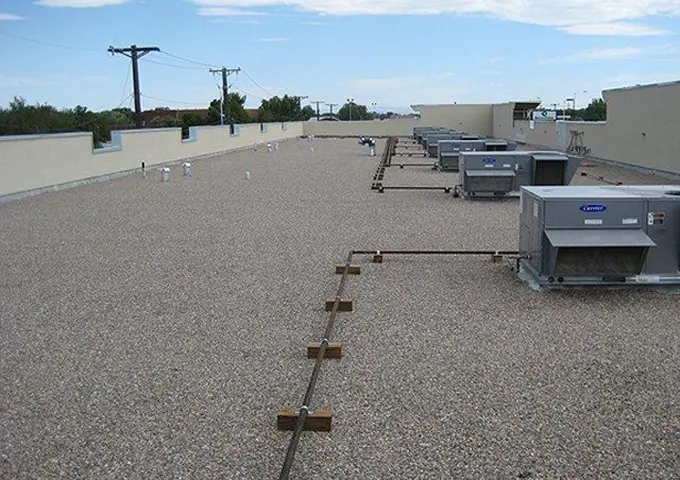
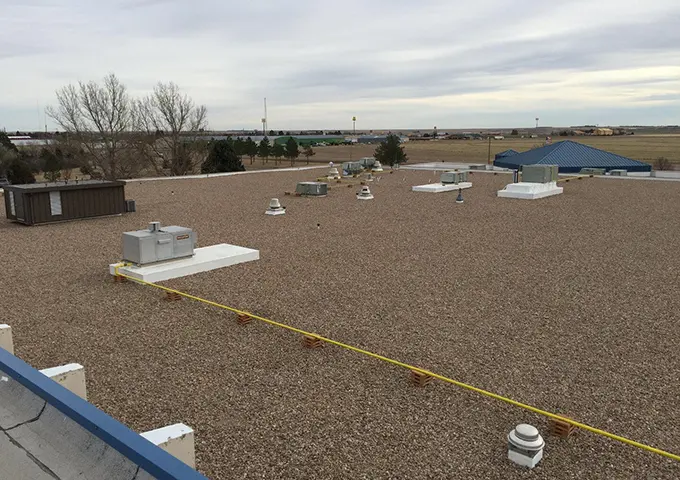
MODIFIED ROOF SYSTEMS
BUILT-UP ROOF SYSTEMS (BUR)
Modified Bitumen (MOBIT) roofing is asphalt-based. It is similar to a Built-up-Roof (BUR) designed for buildings with low-slope or “flat” roof structures. It is made of asphalt combined with polymerized rubber or plastic, then reinforced with fiberglass to create a rugged-yet-flexible waterproof membrane.
Modified bitumen is the evolutionary cousin of the built-up roofing systems (BUR) that have been used on low-slope roofs for more than 100 years.
Engineered modified bitumen roofing membranes originated in Europe in the mid 1960’s and have been used successfully in the United States and Canada since approximately 1975.
The two most common types of modified bitumen roofing are SBS (styrene-butadiene-styrene) and APP (atactic polypropylene). SBS improves the flexibility of the roofing membrane, giving it stronger expansion and contraction capabilities, while APP improves the ability of the roofing system to stay strong as it ages.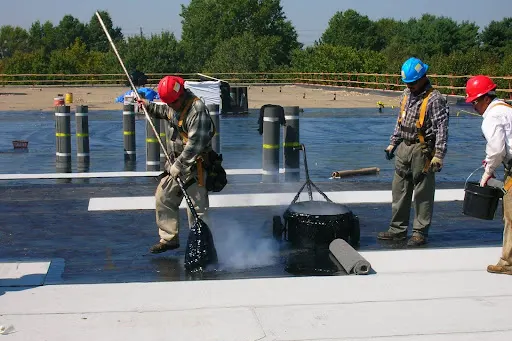
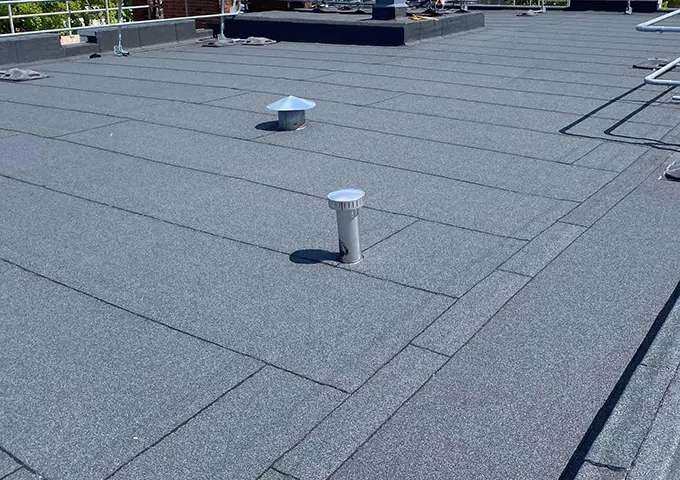
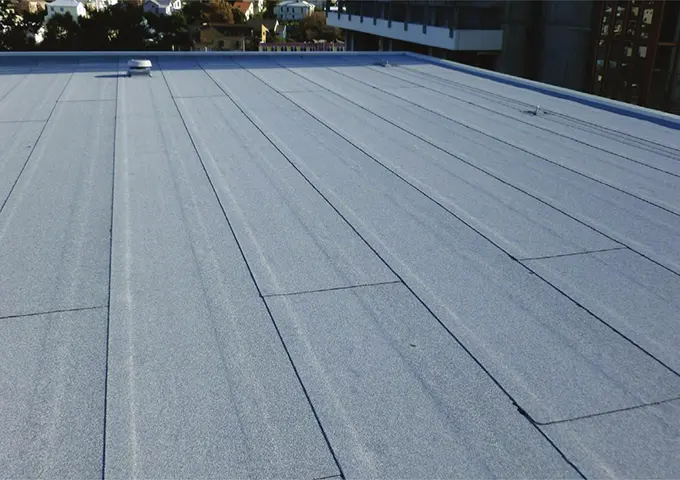
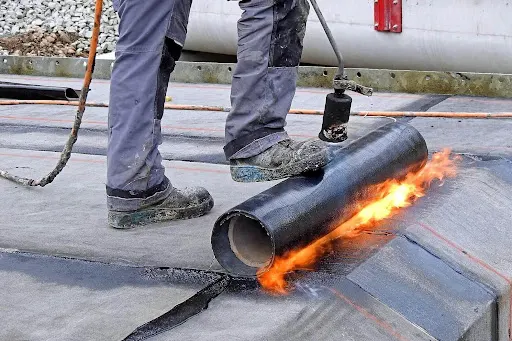
The basic difference between SBS and APP is that APP-modified bitumen is a “plastic asphalt” and SBS-modified bitumen is an “elastic asphalt.” Why? Because APP-modified bitumen is modified with plastic in the form of APP (atactic polypropylene), and SBS-modified bitumen is modified with synthetic rubber in the form of SBS (styrene-butadiene-styrene).
When torching APP roofing membranes, the bitumen begins to flow like candle wax when it reaches temperatures above 300°F. The molten APP-modified bitumen behaves somewhat like hot mopping asphalt, and will flow. On the other hand, SBS-modified bitumen acts differently. While it’s melting point is only slightly lower than that of APP, it doesn’t have the same flow characteristics as APP-modified bitumen. Warm SBS gets very sticky—a factor that increased as additional heat is applied. It is like a gooey paste when it is ready for application. If the heat source remains in contact with the SBS blend, it will eventually begin to flow and be more liquid. By this time, however, it has been overheated.
Because properly heated SBS-modified bitumen doesn’t exhibit a liquid flow, the tendency on the part of the applicator is to give the SBS membrane more heat for a longer period of time than is really necessary. With Tradesman SBSB-modified bitumen roofing materials, determining when the sheet is properly heated is simplified. When the plastic burn-off sheet is melted away, and the SBS-modified membrane has the gooey consistency, the sheet is ready to be rolled into place. Proper torching is easy to check by back-rolling and looking for a full adhesion to the substrate.